Plastic Nameplates in Construction: Labeling Gear and Reducing Risk
Just How Plastic Nameplates Are Made: A Comprehensive Guide to Their Production Process
The production of plastic nameplates entails numerous exact steps, starting from the option of appropriate materials to the final complements. Each stage is crucial, making sure the item meets particular requirements for durability and aesthetic appeals. Different production methods play a substantial duty in crafting these nameplates. Comprehending these processes can clarify the intricacies behind what could appear like an easy product. What factors add to the high quality and personalization of these nameplates?
Understanding Plastic Materials Used for Nameplates

The Style Process: From Principle to Prototype
The design procedure for plastic nameplates starts with a clear idea that guides the total production. Developers team up with customers to specify the objective, design, and details demands of the nameplate. This preliminary phase consists of conceptualizing sessions, mapping out ideas, and picking colors and typefaces that line up with branding goals.Once the principle is developed, designers make use of computer-aided design (CAD) software application to develop in-depth digital representations. These models allow for visualization and adjustments prior to moving on. Comments from stakeholders is essential throughout this stage, as it assists refine the design to meet expectations.After completing the electronic model, a physical model may be generated, often with strategies like 3D printing. This concrete representation allows additional analysis of aesthetic appeals and capability. Generally, the design process is an important action that lays the structure for the reliable manufacturing of high-grade plastic nameplates.
Reducing and Shaping the Plastic
In the cutting and forming phase of plastic nameplate manufacturing, the choice of materials plays a crucial function in determining the end product's top quality and longevity (Plastic Nameplates). Various precision cutting strategies, such as laser cutting and CNC machining, assurance that the plastic is shaped with accuracy and uniformity. This combination of careful material selection and advanced cutting approaches is vital for creating high-quality nameplates
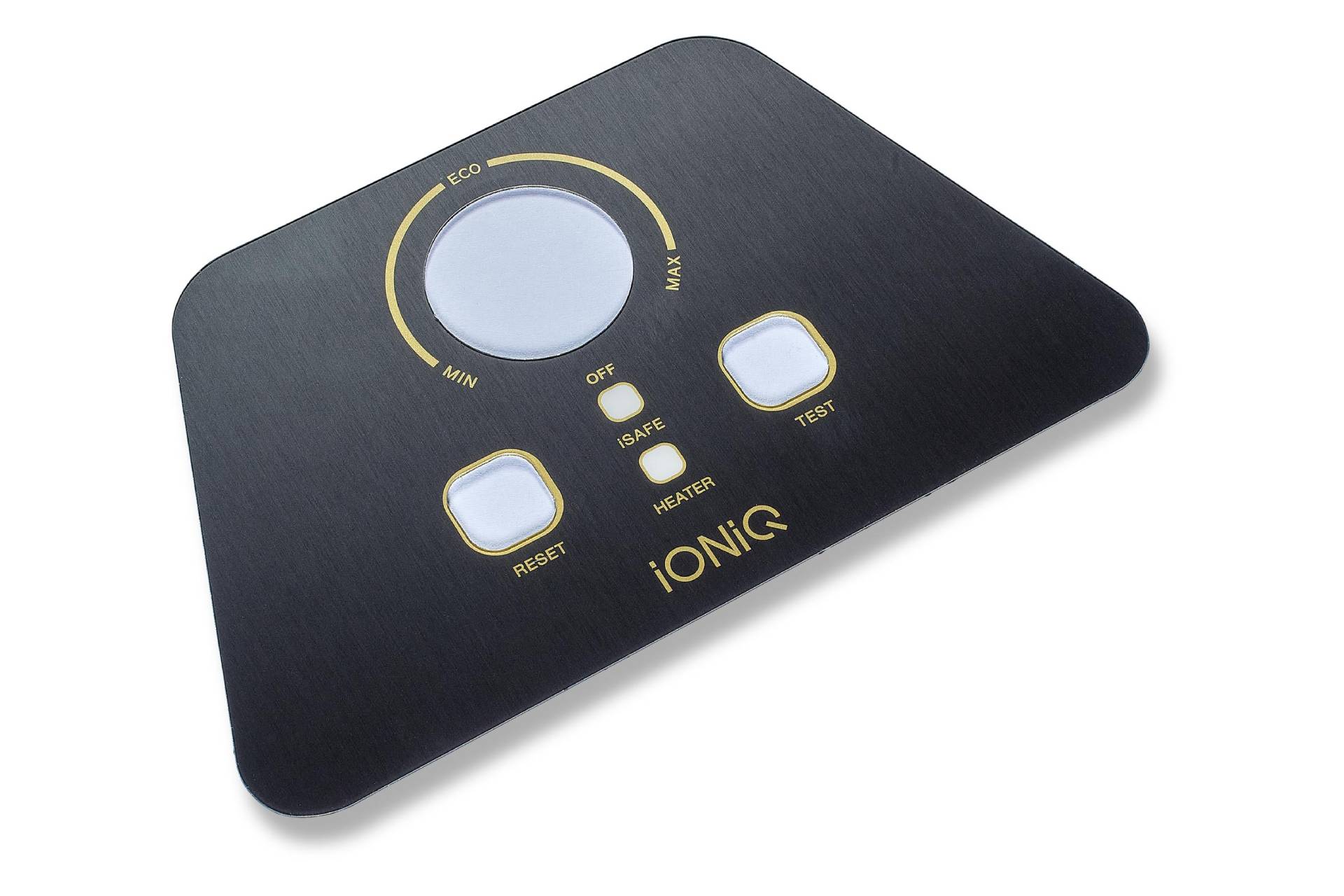
Material Selection Refine
Choosing the ideal product is crucial for generating high-quality plastic nameplates. Various sorts of plastics are readily available, each offering distinct benefits and features. Common selections consist of acrylic, polycarbonate, and PVC. Polymer is favored for its clarity and UV resistance, making it optimal for outdoor applications. Polycarbonate, understood for its resilience and impact resistance, is appropriate for environments that need enhanced protection. PVC is typically picked for its cost-effectiveness and convenience in layout. The choice process additionally thinks about elements such as surface, shade, and density coating, which can substantially affect the final look and functionality of the nameplate. Eventually, the selected product has to straighten with the planned use and visual objectives of the plastic nameplate.
Precision Cutting Techniques
While picking the suitable product lays the groundwork, accuracy reducing methods play a vital function fit the plastic nameplates right into their final types. Different techniques, including laser cutting, CNC milling, and die reducing, are used to achieve precision and consistency. Laser cutting utilizes concentrated light to create clean edges and detailed designs, perfect for complicated patterns. CNC milling provides versatility by eliminating excess product with precision, suiting different densities and forms. Die reducing, on the various other hand, permits mass production of consistent items, improving effectiveness. Each technique is selected based upon the design specs and the desired coating, making sure that the end product meets high quality standards and consumer assumptions while preserving resilience and visual charm.
Printing Strategies for Customization
How can suppliers achieve lively and specific designs on plastic nameplates? The response hinges on different printing techniques customized for customization. Digital printing has gained popularity as a result of its capacity to produce intricate designs and high-resolution photos directly onto plastic surface areas. This approach enables fast turnaround times and very little configuration expenses, making it ideal for short runs and personalized orders.Screen printing stays another commonly made use of technique, particularly for larger amounts. It involves producing a stencil and using layers of ink, resulting in rich colors and durability. UV printing, which utilizes ultraviolet light to treat the ink, is likewise efficient, supplying excellent adhesion and resistance to useful site fading.Additionally, pad printing uses flexibility for irregularly shaped nameplates, permitting thorough layouts on tough surfaces. These printing methods allow makers to satisfy varied customer needs while guaranteeing high quality and durability in their plastic nameplate products.
Surface Therapies and Finishing Options
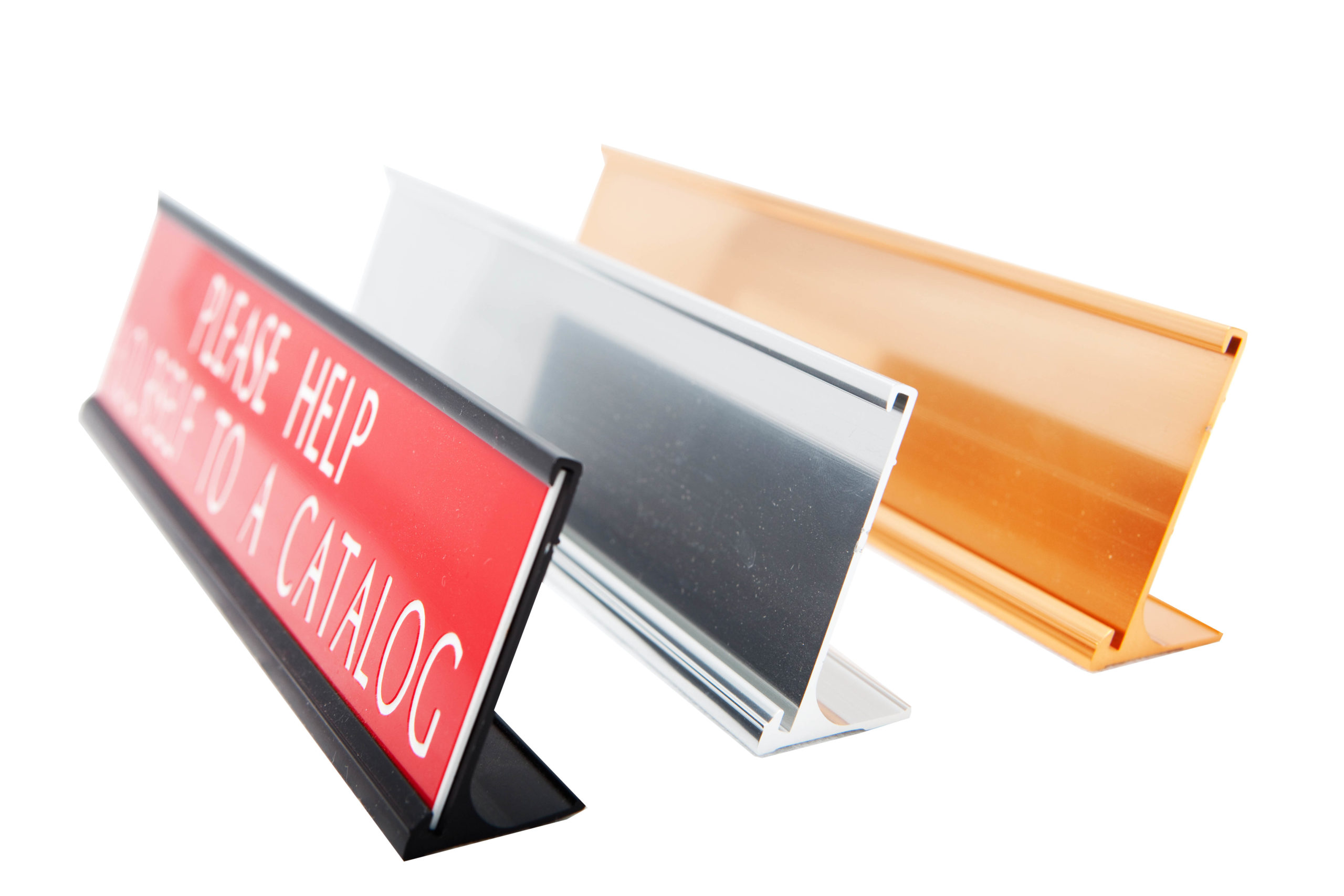
Quality Assurance Measures in Production
Ensuring the highest criteria of quality assurance throughout the production of plastic nameplates is vital for preserving product integrity and consumer fulfillment. Manufacturers implement strenuous inspection procedures at different phases of the production procedure. Initially, raw materials go through extensive testing to verify they satisfy requirements for longevity and color consistency. Throughout the molding phase, automated systems keep track of parameters such as temperature and stress to protect against defects.In enhancement, visual inspections are performed to determine any surface area blemishes or misalignments. When the nameplates are produced, they undergo functional examinations, consisting of bond tests for printed components and anxiety examinations for resilience. Quality control groups frequently employ analytical tasting techniques to assess sets, making certain that any discrepancies from requirements are quickly addressed. This detailed approach not only boosts product quality however likewise promotes trust with customers, verifying the producer's dedication to quality in every nameplate created.
Product packaging and Circulation of Finished Nameplates
The packaging and circulation of finished plastic nameplates are important actions in ensuring they get to customers in suitable condition. Various packaging materials are chosen to safeguard the nameplates during transportation, while shipping approaches are thoroughly chosen based upon performance and cost-effectiveness. Furthermore, efficient storage space solutions are carried out to maintain high quality up until the nameplates are supplied.
Product Packaging Materials Made Use Of
Picking proper packaging products is necessary to ensure their defense throughout transit when dispersing ended up plastic nameplates. Generally employed products include bubble wrap, foam cushioning, and cardboard boxes, all developed to cushion the nameplates versus impacts and shocks. Bubble wrap provides a flexible obstacle, while foam cushioning assurances that nameplates remain securely in place, reducing the threat of scrapes or breakage. Additionally, tough cardboard boxes are used to have the nameplates, using architectural assistance and defense from external components. Labels might be put on indicate dealing with instructions or vulnerable components, better enhancing security during transportation. Overall, making use of top quality packaging materials substantially adds to the honesty and presentation of the finished plastic nameplates upon arrival at their destination.
Delivering Methods Used
Effective distribution of ended up plastic nameplates relies upon numerous shipping approaches from this source that guarantee secure and prompt distribution. Firms frequently make use of courier solutions, freight delivery, and post offices, depending on the size, weight, and destination of the plans. For regional shipments, courier services provide fast transit, making sure nameplates get to clients rapidly. For bigger orders, freight delivery is favored, making use of vehicles or shipping containers to transport bulk quantities effectively. Post offices work as a cost-effective choice for smaller sized shipments, particularly for domestic shipments. All shipping techniques focus on safety packaging to avoid damages during transportation. Tracking systems are also used to keep an eye on shipments, offering customers with real-time updates and confidence regarding the condition of their orders.
Storage Space Solutions Implemented
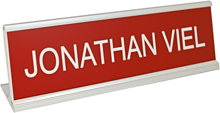
Regularly Asked Concerns
What Sorts Of Businesses Commonly Utilize Plastic Nameplates?
Plastic nameplates are frequently made use of by various organizations, consisting of offices, hospitals, schools, and factories. These nameplates offer important functions such as recognition, info display, and branding, adding to organizational efficiency and expert look across diverse atmospheres.
The length of time Does the Entire Production Process Take?
The manufacturing procedure period varies based on intricacy and amount, typically varying from a couple of days to a number of weeks. Elements affecting this timeline include layout authorization, material accessibility, and manufacturing strategies utilized by the company.
Can Plastic Nameplates Be Recycled After Usage?
Plastic nameplates can be recycled, supplied they are made from recyclable materials. However, the schedule of recycling programs and regional guidelines might impact their recyclability. Correct disposal methods are vital to guarantee efficient recycling.
What Are the Environmental Impacts of Plastic Nameplate Production?
The ecological influences of plastic nameplate production include carbon emissions, resource deficiency, and contamination from manufacturing procedures. Plastic Nameplates. In addition, improper disposal contributes to plastic waste, detrimentally affecting communities and wildlife, highlighting the requirement for sustainable methods
Exist Any Type Of Safety And Security Worry About Plastic Nameplates?
Safety and security worries relating to plastic nameplates largely involve possible chemical direct exposure throughout production and the risk of materials weakening in time, which may bring about dangerous substances being launched, affecting both human health and wellness and the atmosphere. While various materials can be made use of for nameplates, plastic continues to be a prominent option due to its versatility and resilience. In the cutting and forming stage of plastic nameplate manufacturing, the option of products plays a necessary role in determining the last item's quality and resilience. Choosing the ideal material is necessary for generating high-grade plastic nameplates. While picking the proper material lays the foundation, accuracy cutting strategies play an important duty in shaping the plastic nameplates right into their final kinds. When distributing completed plastic nameplates, choosing suitable packaging products is crucial to guarantee their security throughout transit.